HotSpot: Thermal Seeking

Software
Future Developments
The restricted data package size that the Bluetooth can transmit also limited the number of discrete sectors that our system could resolve. By implementing a different communication protocol, the system would be able to differentiate between smaller regions. ​
In order to achieve better precision in our positioning system, the software could implement a feedback control scheme whereby the desired position is subtracted form the measured location in order to compute a distance error which gets fed into a controller to drive position error to zero.

Mechanical
Future Developments
With more resources and a higher budget, an obvious improvement would be to integrate tighter-tolerance materials and more refined mechanisms. Materials like aluminum and steel can be held to better tolerances and are more structural which would both contribute to a more robust system. Additionally, implementing better motors for a belt and pulley system which rides on linear bearings would make the motion smoother.
One possible scaling of this technology is UAV imaging for search-and-rescue operations.
HotSpot
System Limitations
After extensive testing, we discovered one limitation in our current design. Namely, because there is approximately one inch of overlap between successive thermal image captures, an object that lies within this band will be counted in multiple sectors. The design of the current implementation is that we iterate over the temperatures in such a way that the system will return to whichever sector has the highest recorded temperature. Because of inherent fluctuations in the FLIR camera's temperature readings, the system will occasionally return to a sector that appears to contain only a small part of the hot object. Although this result is consistent with the logic of our code and completes the goal, it presents a non-ideal solution.
Challenges
Software
Accessories plugged into the iPhone lightening port prevent active coding debugging feedback
The learning curve of new programming languages and frameworks slows down project development
Incomplete SDK documentation hinders implementation
Debugging interconnected electromechanical systems introduces unforeseen challenges
Bluetooth communication channel is limited to 16 binary commands
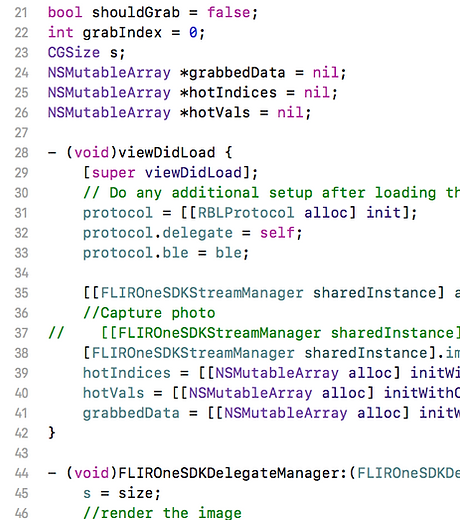
Challenges
Hardware
Inherent tolerancing limitations of laser cutting introduces errors in part dimensions
After cutting, wooden parts tend to warp slightly which leads to internal stresses in glued assemblies
Smooth motion depends on the travel gear flanges not binding with the gear rack and the axle remaining perpendicular to the X-direction of motion
Improper belt tension can cause the motors to stall or the drums to slip
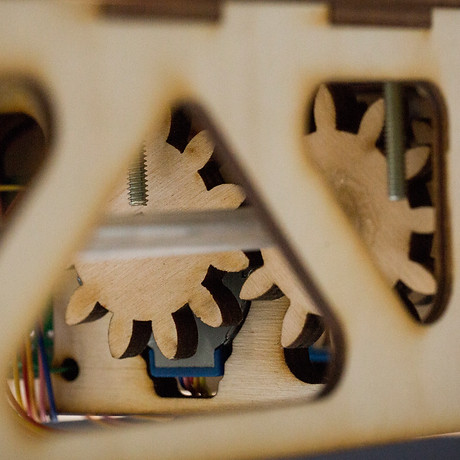
Reflections
​
From beginning to finish, HotSpot has challenged us to innovate mechanical designs, devise integrated code and assimilate a complex mechatronic system. We've come a long way since our inception fifteen weeks ago and have seen our design evolve from back-of-the-envelope sketches to a robust and unified project. We're proud of the result and believe that this project has the potential for future growth.
​
The ultimate goal of this project was to scan a region, identify the hottest object and return to this location. After weeks of design, development and testing, HotSpot completes its task in a mere two-and-a-half minutes. Although future steps exist to improve the mechanism's resolution, it nonetheless consistently returns to the detected object's sector.
​
The initiative for this project was to develop a system implementing sensing, planning and actuation. Sensing is completed by the onboard FLIROne thermal imaging camera. After each image is captured, it is transmitted to the iPhone where the temperature of the hottest object is extracted and recorded. The planning phase is completed by the iPhone at the conclusion of the scanning sequence. Here, the iOS application computes the sector with the highest recorded temperature and passes the location as a byte via Bluetooth to the RedBear board. At this point, the actuation phase commences and the RedBear evaluates the necessary motions to reach the target. Commands are sent from the microcontroller to the motors and the payload moves to this location.
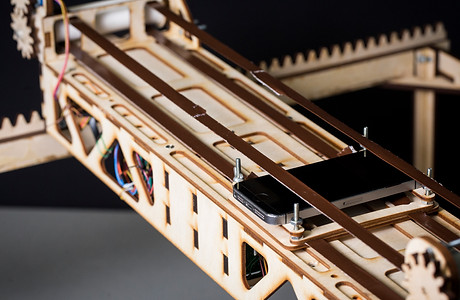